In a course called "user-centred product design", my aim was to develop an aesthetic sex toy for men that would remove the taboo from the subject and at the same time open up new concepts for circularity in the hygiene sector. To begin with, I analyzed existing products, talked to a store owner and read scientific papers on the subject of sexuality. I then defined market segments and worked out possible weaknesses of competing products. This crystallized the need for an independent design language without sexist references to the female body - combined with good cleanability, variants for different penis sizes and a focus on sustainability.
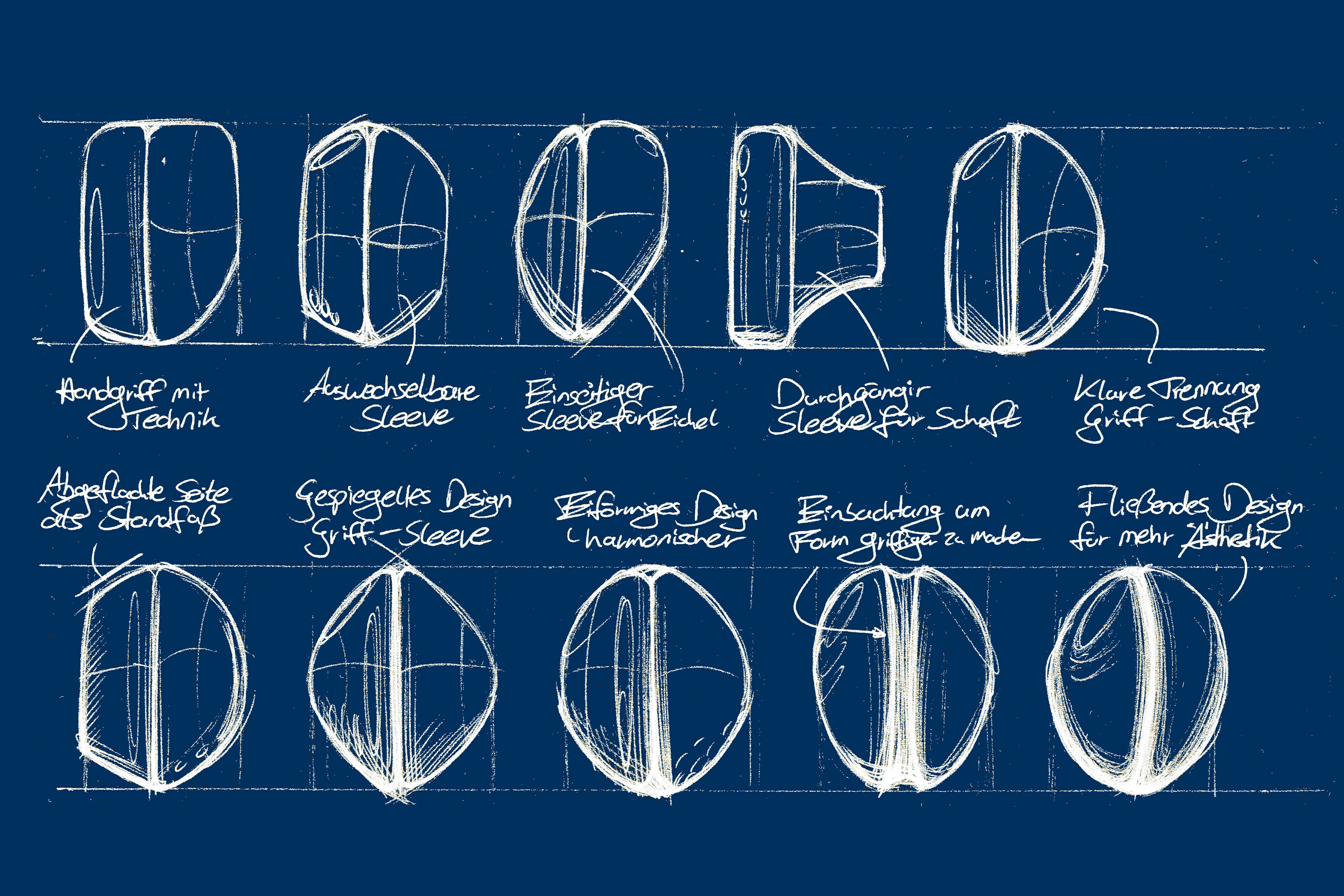
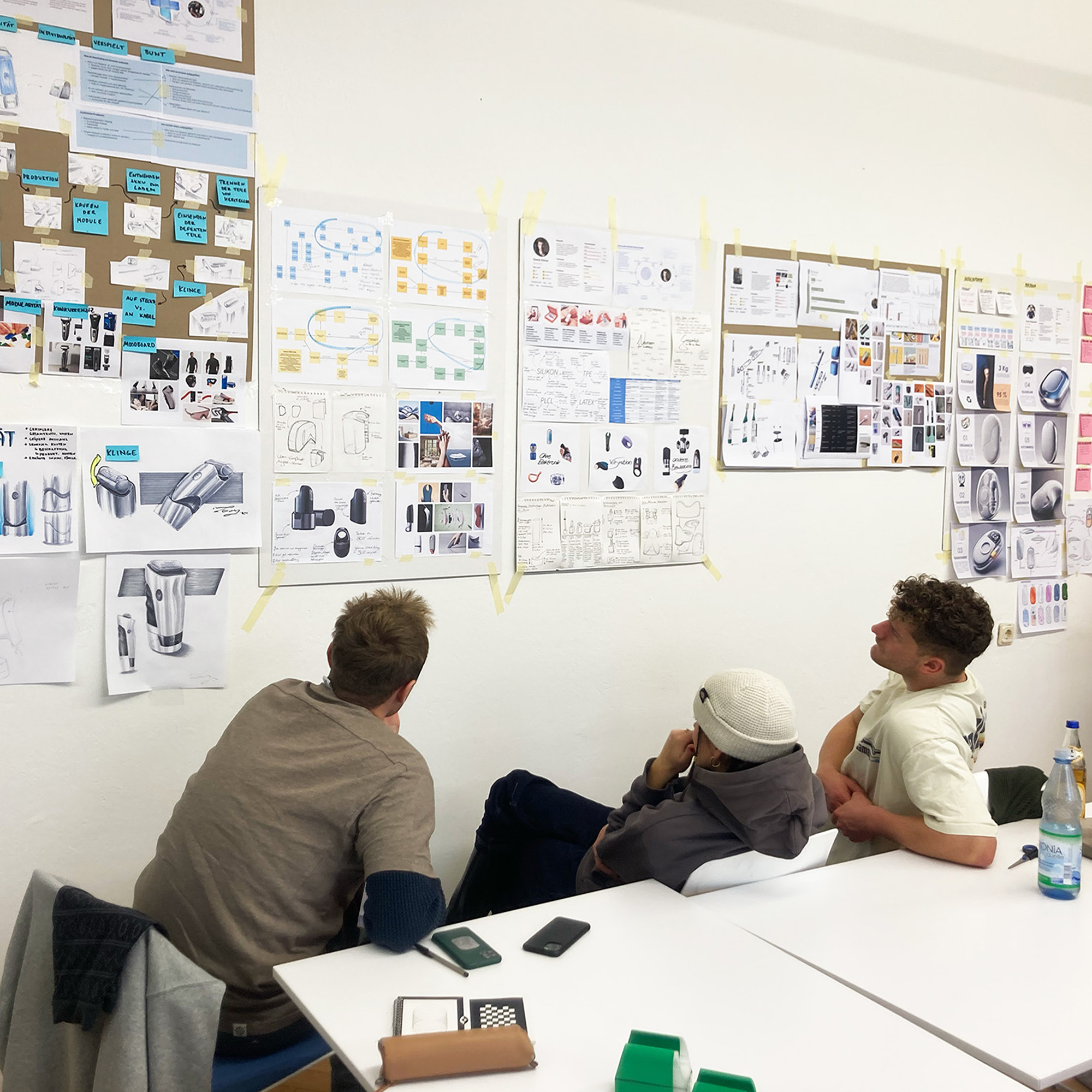
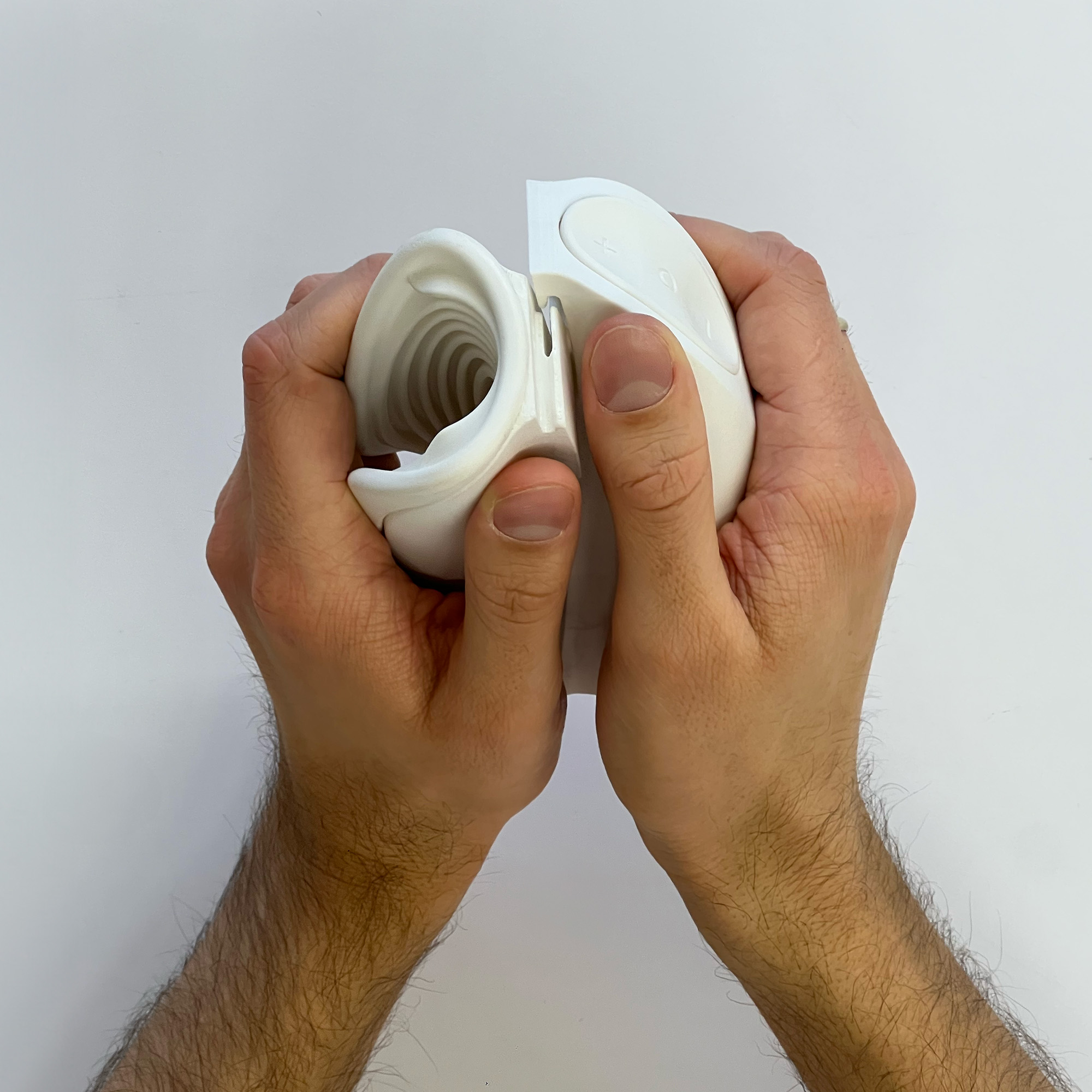
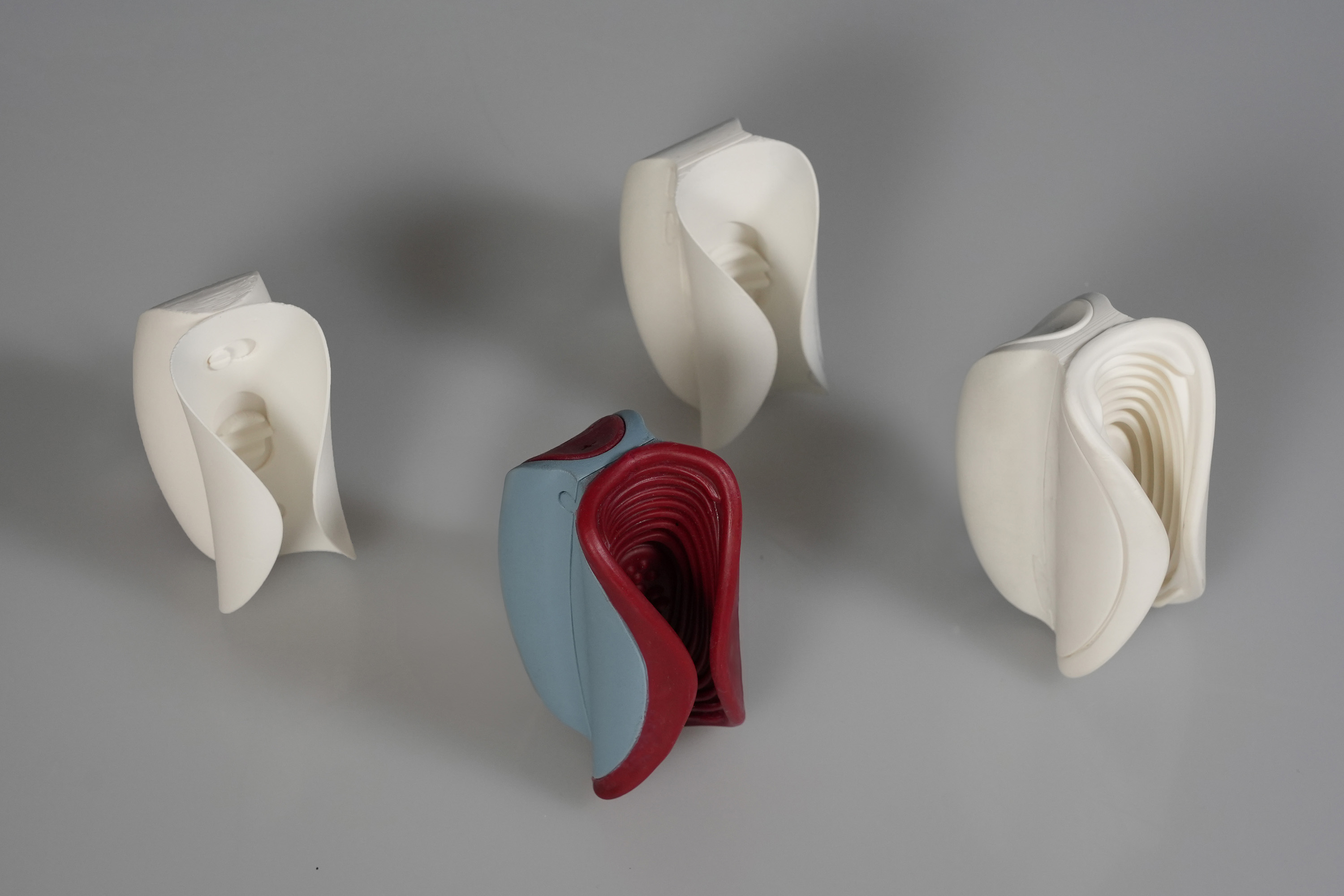
In the design phase, the focus was on ergonomic studies to find shapes that fit well in the hand. With the help of clay models, I developed the first prototypes, accompanied by sketches and research into suitable technology. I collected all the materials, analyses and designs on large cardboard walls and discussed them in regular feedback rounds. Using CAD models and 3D prints, I was able to check the designs and gradually develop them further.
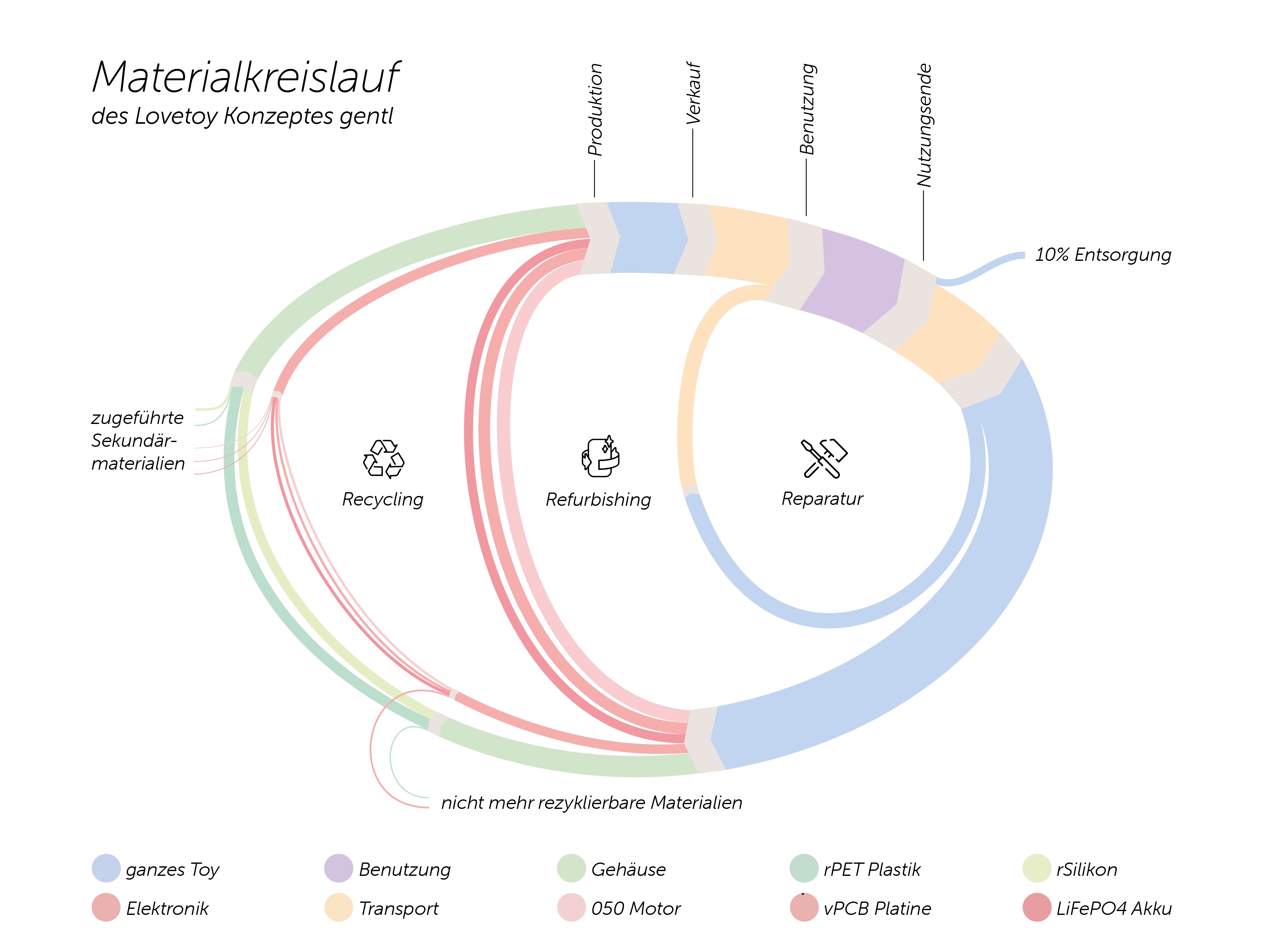
During my research, I noticed that many comparable products are designed as purely disposable items. To counteract this, with gentl I focused on three circular principles: Recycling, refurbishing and repairing (see graphic above). In the recycling cycle, PET and silicone are automatically separated after being returned: cast-in perforations enable residue-free separation of the materials, which are then sterilized and processed. The PET is granulated and the silicone is recycled (e.g. via New Dawn Silicones). Both materials can now be reused for the original component. Electronic components (vPCB, 050 motor, LiFePO4 battery) go through the refurbishing cycle, as these usually have a significantly longer service life: Batteries with over 80% remaining capacity (up to 2000 charging cycles), for example, are checked and reused. The repair cycle enables defective standard parts to be replaced thanks to a fully dismantlable design. A deposit system and low-cost repairs increase the return rate. New material comes exclusively from secondary sources in order to conserve primary raw materials. This can ensure a cycle with 87% material circulation, which would be unique in the hygiene sector.
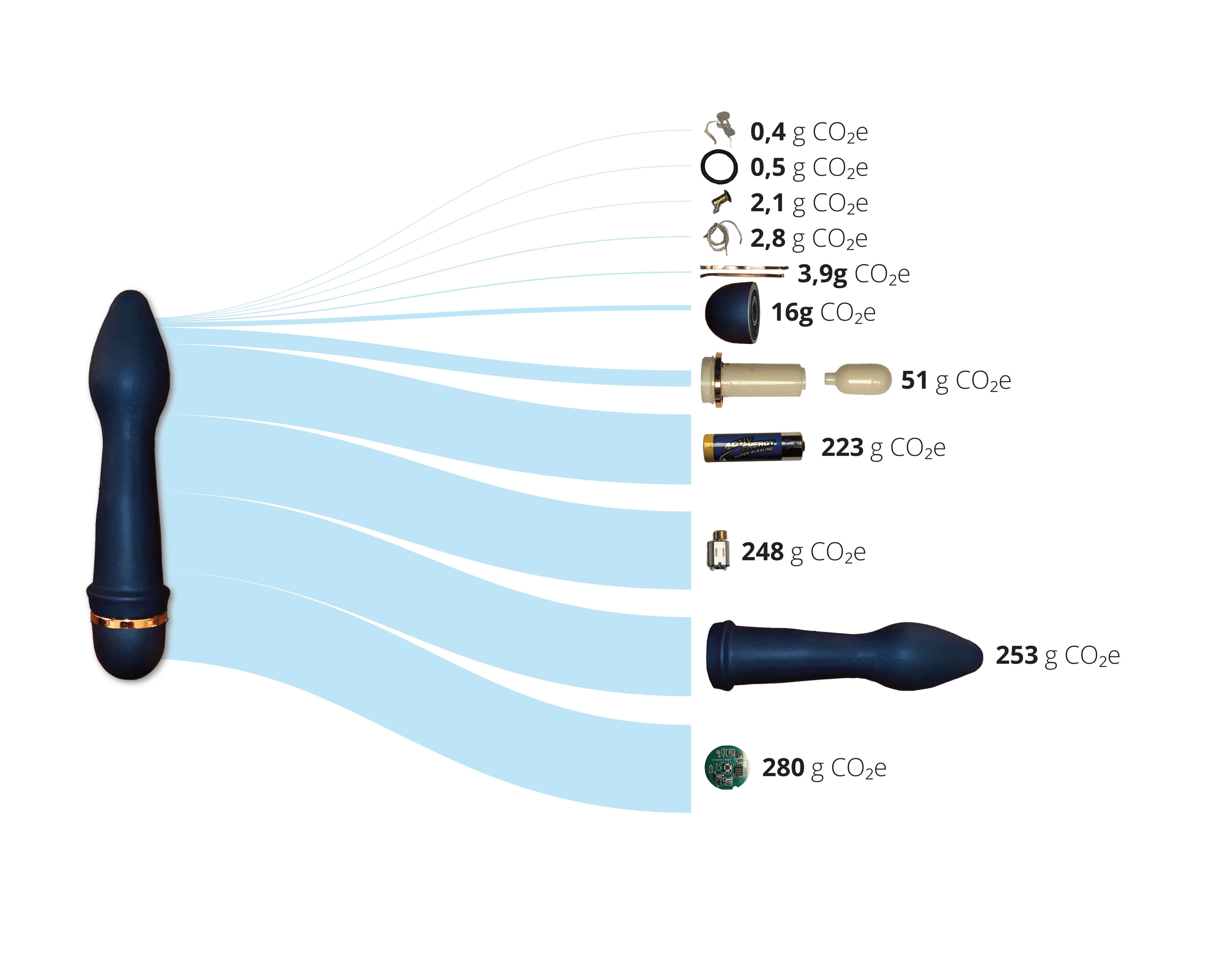
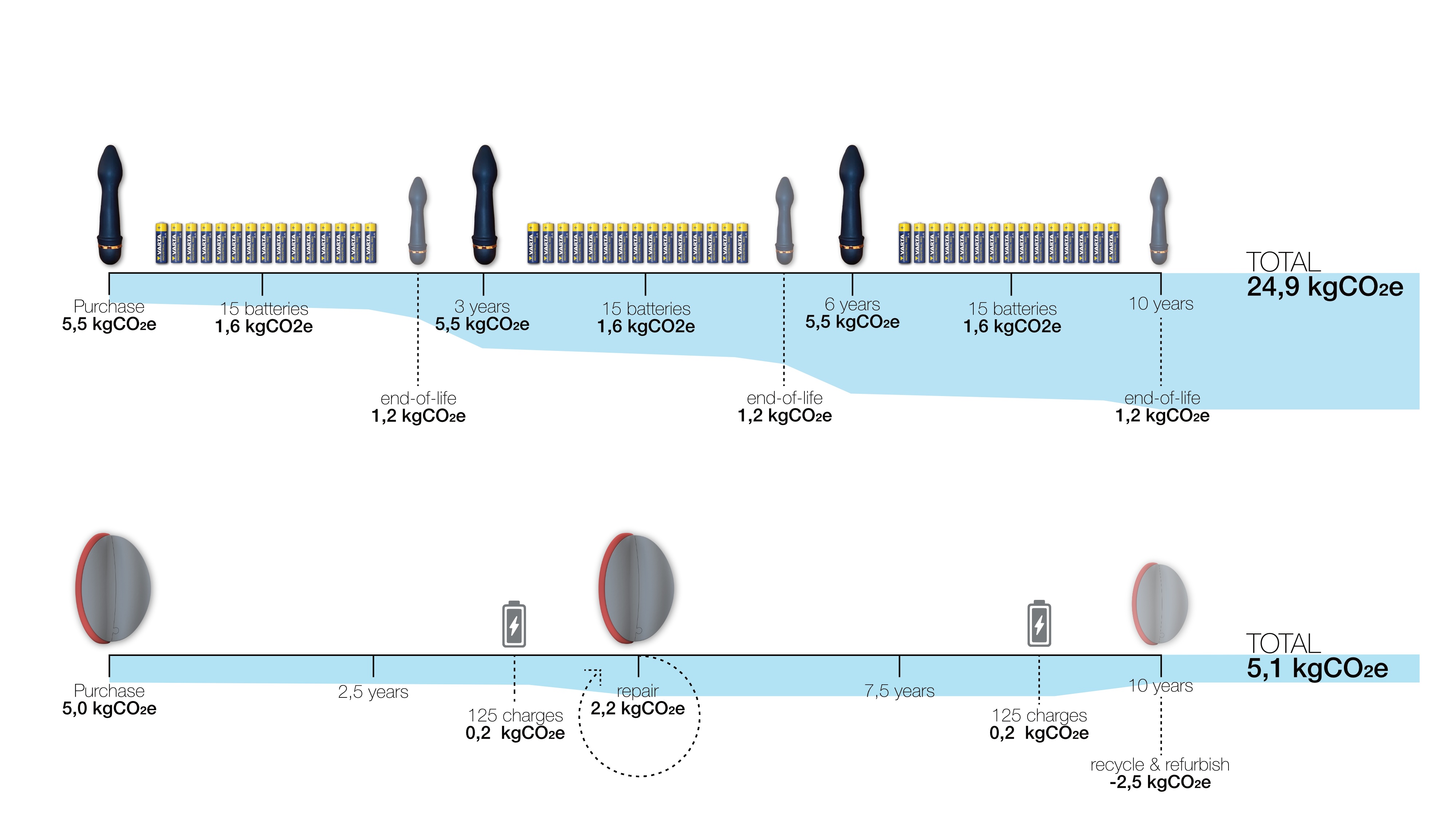
To determine the emission hotspots, I disassembled a reference product, weighed the individual parts and analyzed them in terms of their CO₂ emissions using external LCA data. Although the system limits were tight and the values tended to be too low as a result, it was clear to see which areas caused the highest emissions. I then compared my concept with its repair and reuse strategies to the reference product. Over a period of ten years, the conventional toy would have to be bought three times on average, whereas gentl remains in use for much longer thanks to its repairability and greater durability - and therefore has a much better environmental footprint.
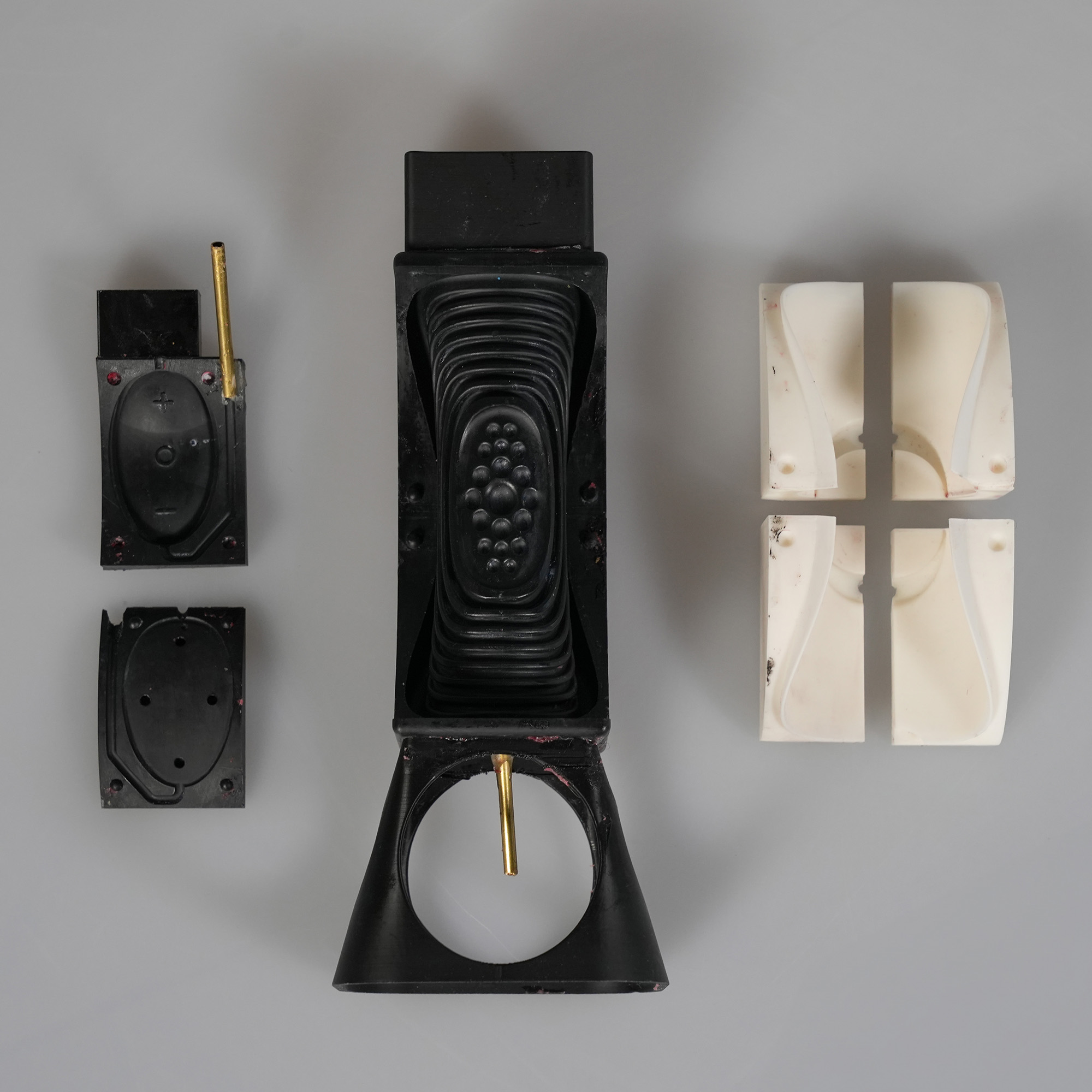
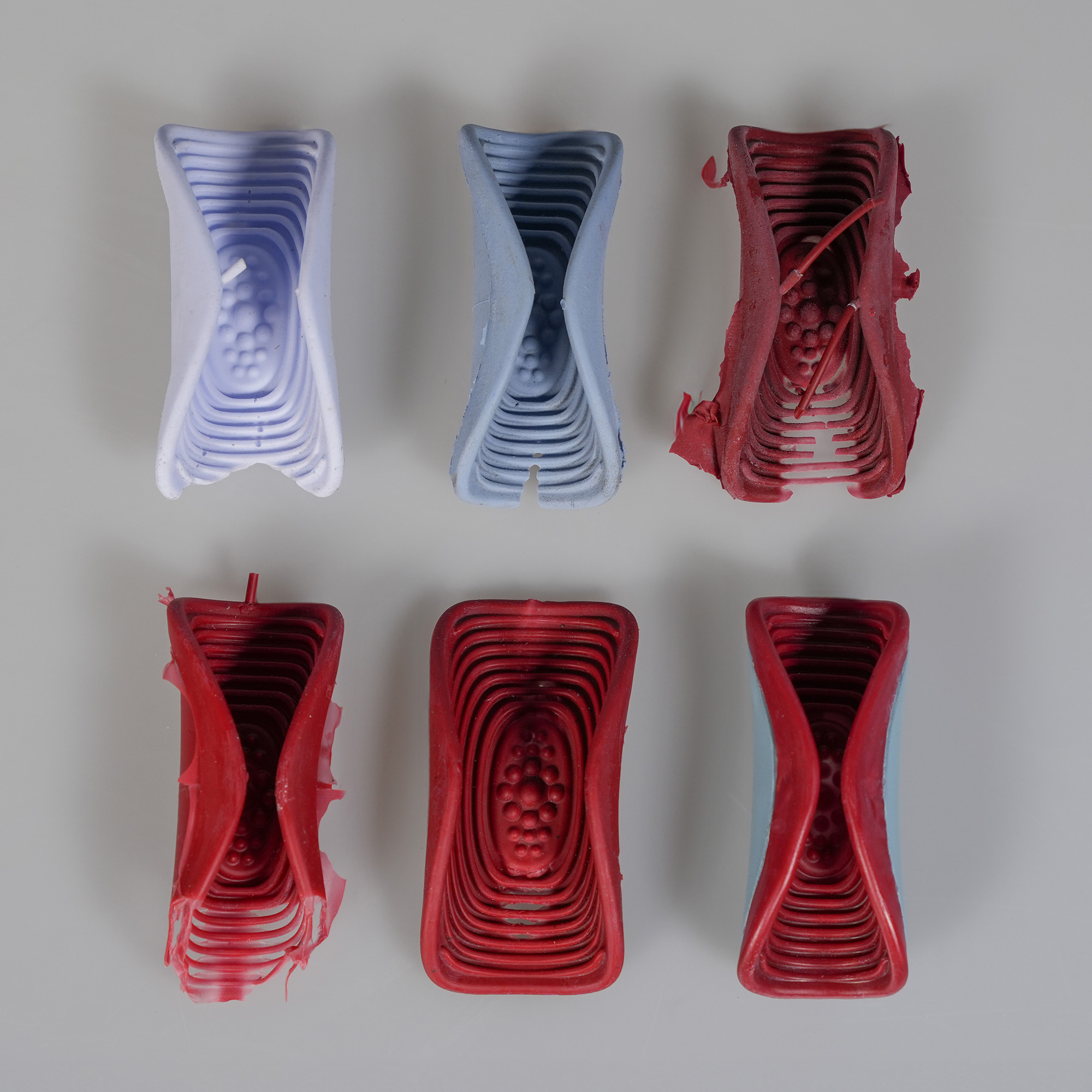
Another important issue was to connect the silicone and the PET housing in such a way that the connection would hold securely throughout the entire usage phase and could be separated again later during production. As the body was to be made exclusively from two materials without additives, I did not use glue. Instead, I developed cast-in perforations in the silicone that are robust enough to withstand use, but can be separated from each other by machine in the factory. Prototyping with silicone was also a challenge: the molds were relatively complex and the entire casting process had to be done under vacuum to avoid bubbles.
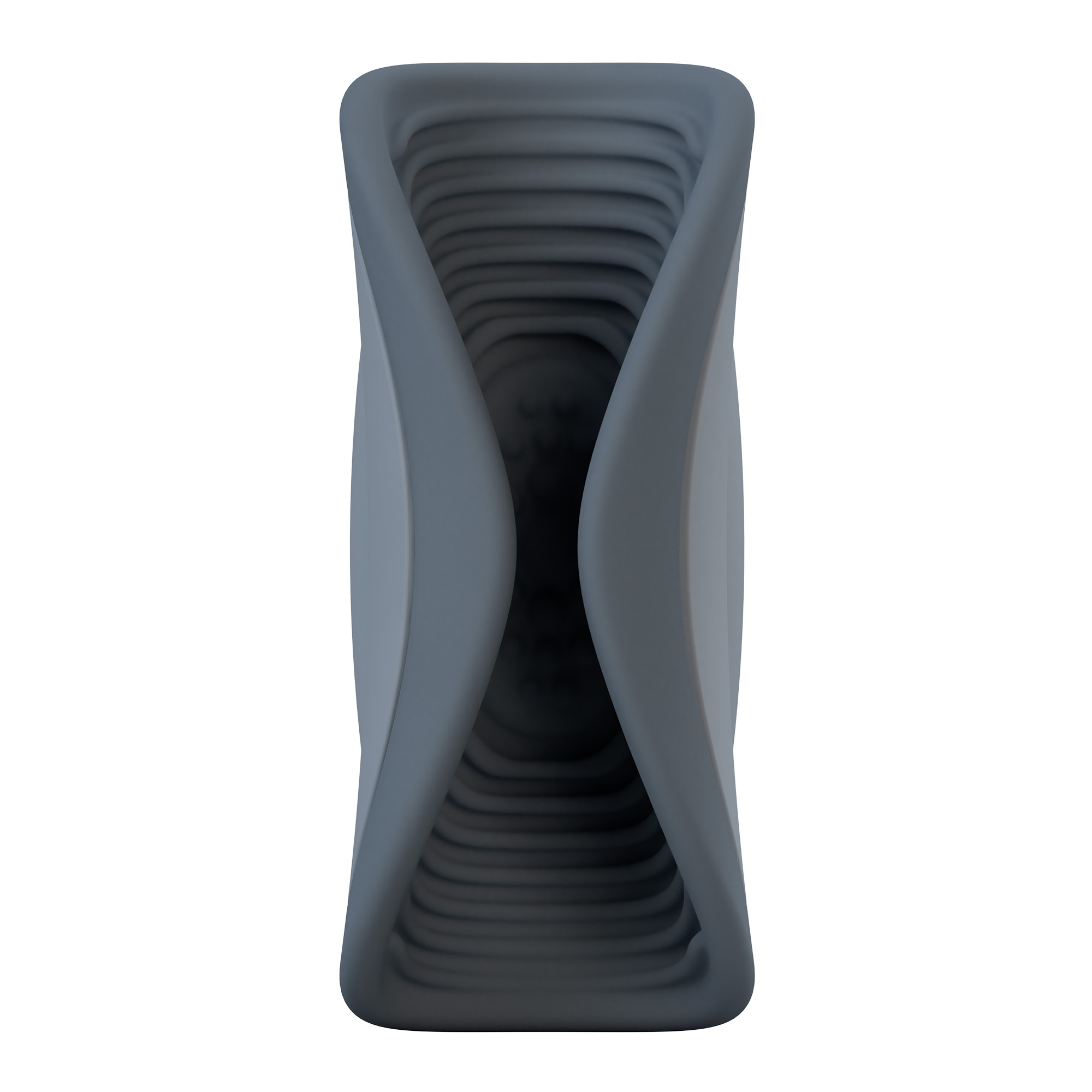
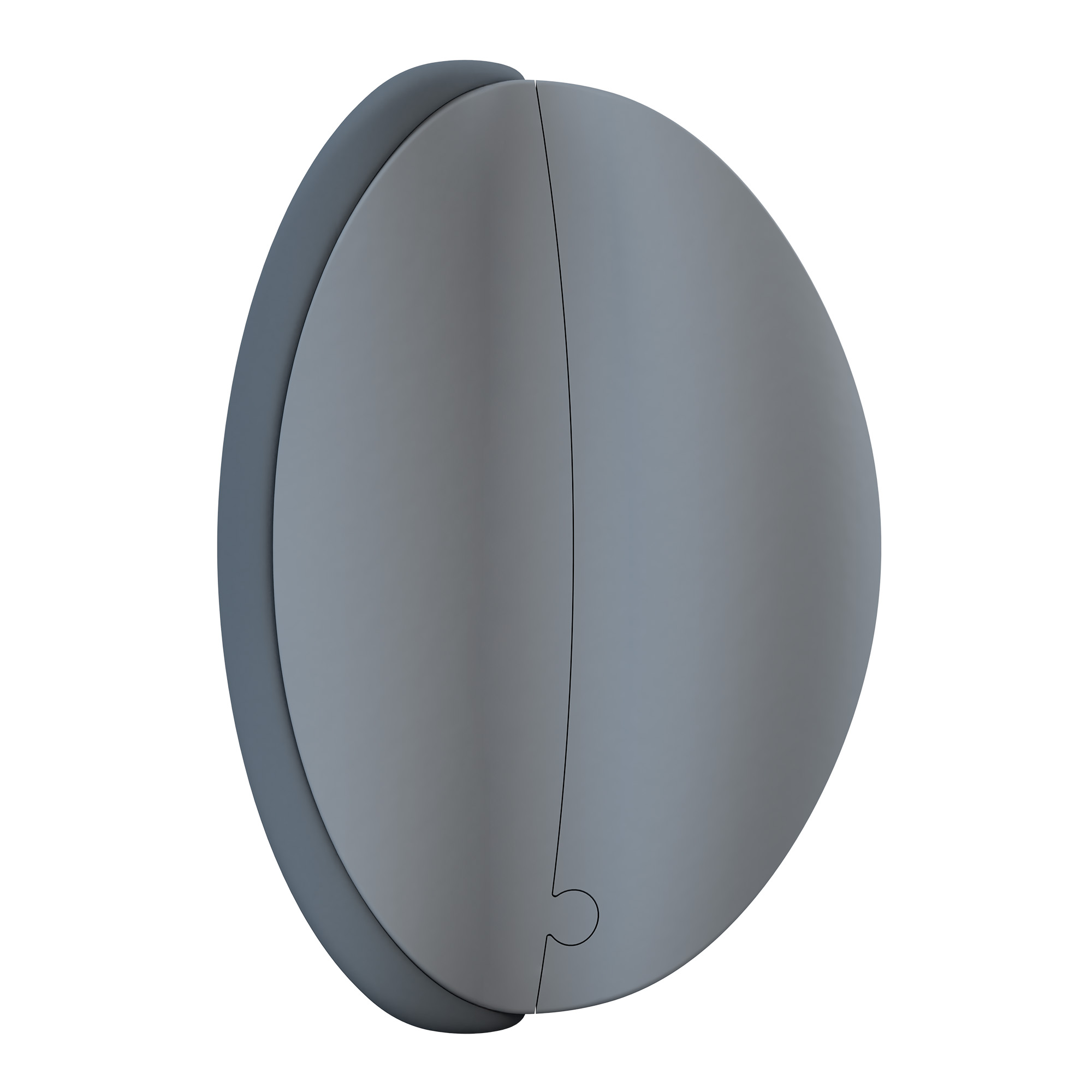
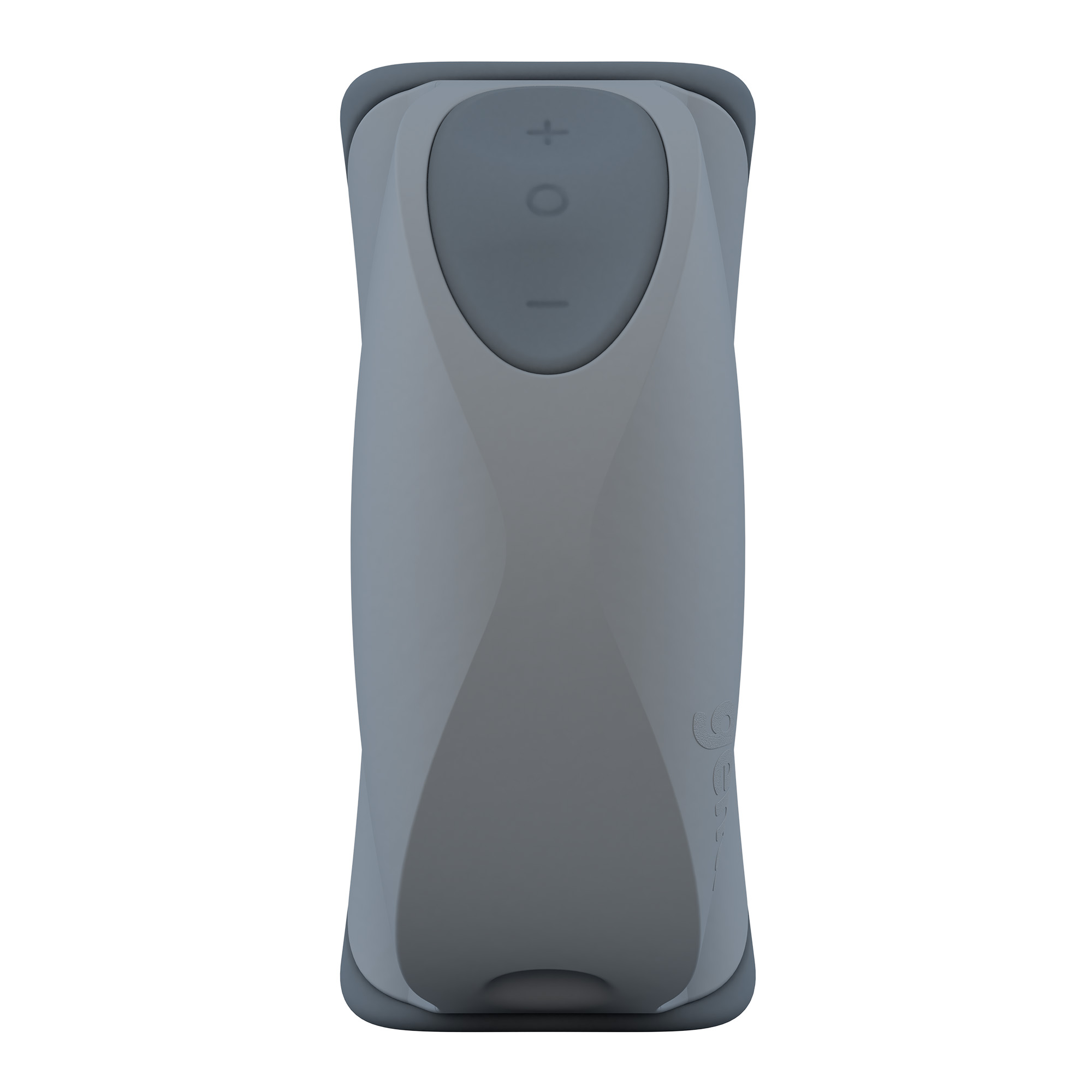
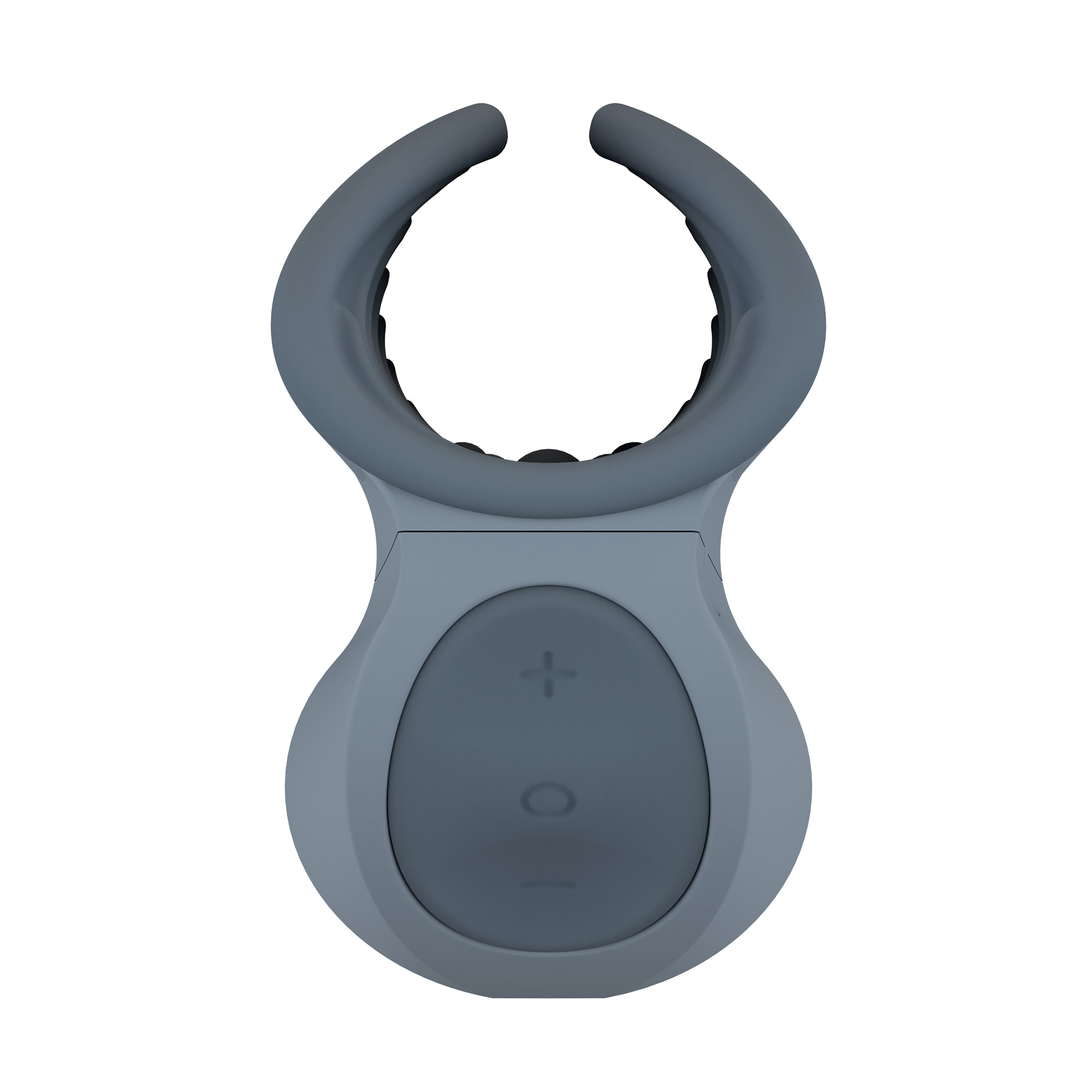
I developed an independent, reduced and ergonomic design language for gentl, free of clichés. The gender-neutral design deliberately avoids sexist body references and a typically masculine, technical aesthetic. With this design, I want to bring love toys for men out of a stigmatized corner and into the realm of responsible self-care - gentl does not have to be hidden away in a drawer. The handle with integrated technology can be combined modularly with interchangeable front parts made of recycled PET and silicone, which are available in different sizes and textures. As these front parts wear out more quickly, they can be replaced separately, reducing waste and enabling long-term use.
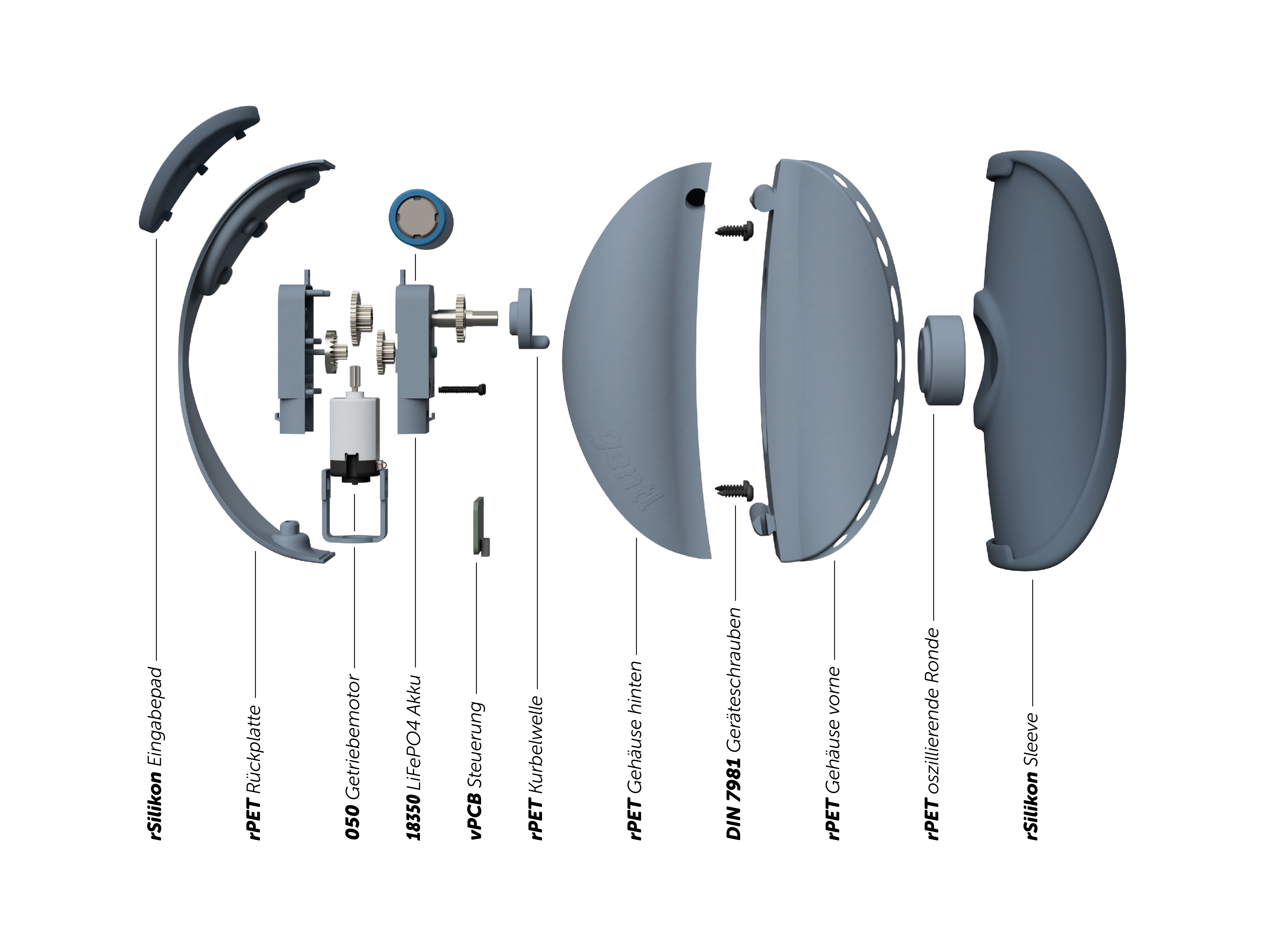
How a love toy feels is important. The market is often dominated by vibrators that are too high-frequency and not intense enough, or very large devices with sliding mechanisms that offer a good sensation but are bulky and not durable. To find a middle ground, I first tested different approaches with electromagnets and Arduino controllers. In the end, I decided on a geared motor with a slider crank that generates an oscillation of about 10 millimeters. The movement is transmitted directly to the silicone insert and provides dynamic and intense stimulation. This mechanism I developed is much more compact, robust and durable than the established products.
All components are screwed or push-fitted. Screws, motor and battery are standard components, which makes repairs easier and reduces the carbon footprint through efficient production. For the controller, I chose a vPCB board, which is much easier to repair than conventional FR-4 boards and can be largely recycled at the end of its service life.
Idea, design and technical concept: Jakob Volkmer. This intellectual property is subject to copyright (§§ 1, 2 UrhG). Use, duplication or further distribution without express permission is not permitted.
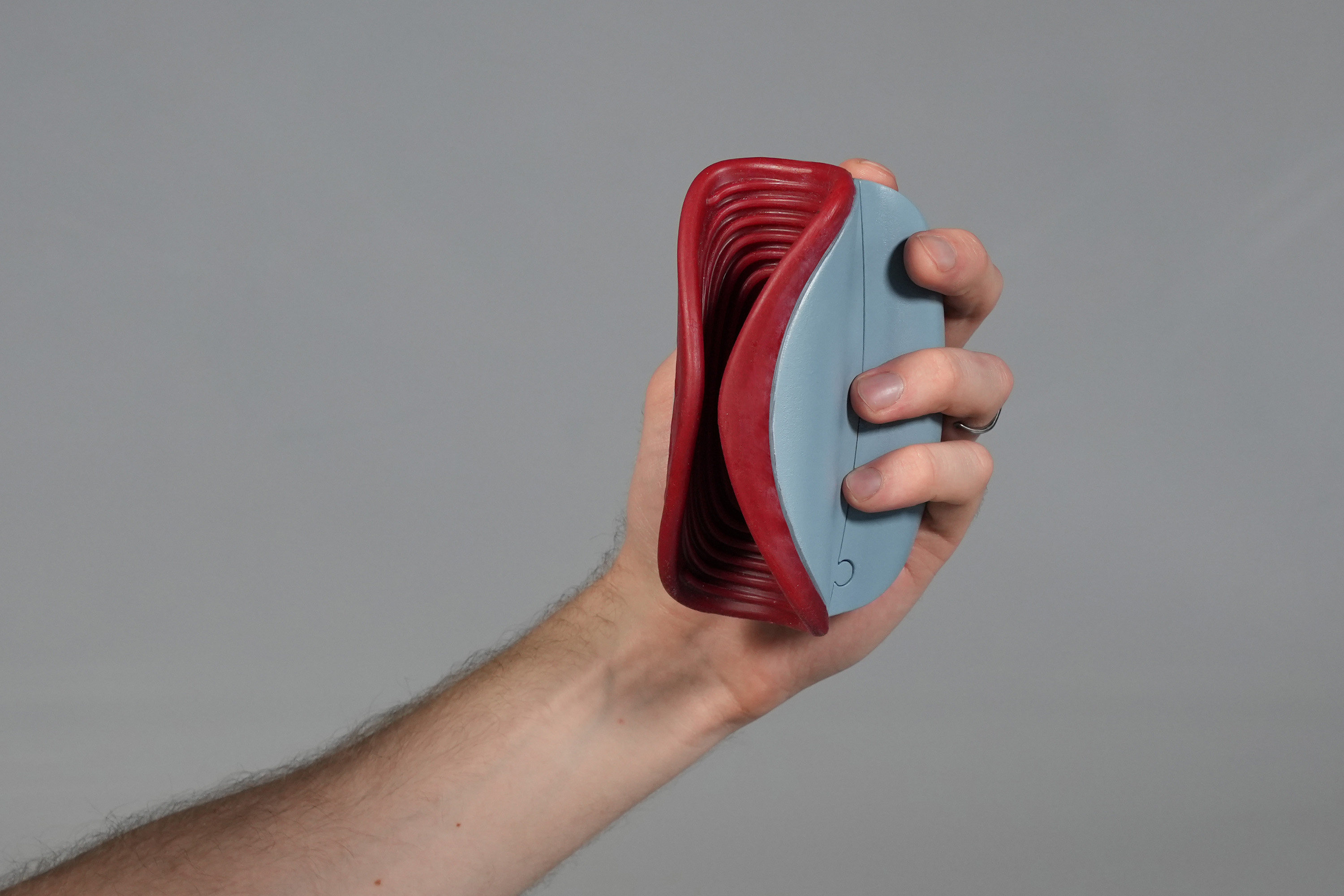